Destylarka do rozpuszczalników to urządzenie, które wykorzystuje proces destylacji do oddzielania różnych substancji chemicznych na podstawie ich temperatury wrzenia. W praktyce oznacza to, że rozpuszczalniki mogą być oddzielane od zanieczyszczeń lub innych składników, co jest niezwykle istotne w wielu branżach, takich jak przemysł chemiczny, farmaceutyczny czy kosmetyczny. Proces ten polega na podgrzewaniu cieczy do momentu, w którym zaczyna ona parować, a następnie schładzaniu pary, aby skondensować ją z powrotem w cieczy. Dzięki temu możliwe jest uzyskanie czystych substancji o wysokiej jakości. Destylarki różnią się konstrukcją oraz zastosowaniem, od prostych modeli laboratoryjnych po bardziej zaawansowane systemy przemysłowe. W laboratoriach często stosuje się destylarki szklane, które umożliwiają dokładne monitorowanie procesu destylacji, podczas gdy w przemyśle używa się bardziej wytrzymałych materiałów odpornych na działanie agresywnych substancji chemicznych.
Jakie są rodzaje destylarek do rozpuszczalników i ich funkcje
Na rynku dostępnych jest wiele różnych typów destylarek do rozpuszczalników, które różnią się zarówno budową, jak i przeznaczeniem. Najpopularniejsze modele to destylarki proste, frakcyjne oraz próżniowe. Destylarki proste są najczęściej używane w laboratoriach i charakteryzują się prostą konstrukcją oraz łatwością obsługi. Umożliwiają one oddzielanie substancji o znacznej różnicy temperatur wrzenia. Z kolei destylarki frakcyjne są bardziej skomplikowane i pozwalają na separację wielu składników jednocześnie dzięki zastosowaniu kolumny frakcyjnej. Tego typu urządzenia są idealne do oczyszczania rozpuszczalników o zbliżonych temperaturach wrzenia. Destylarki próżniowe natomiast działają w obniżonym ciśnieniu, co pozwala na destylację substancji w niższych temperaturach, co jest szczególnie ważne dla substancji wrażliwych na wysoką temperaturę.
Jakie materiały są wykorzystywane w budowie destylarek do rozpuszczalników
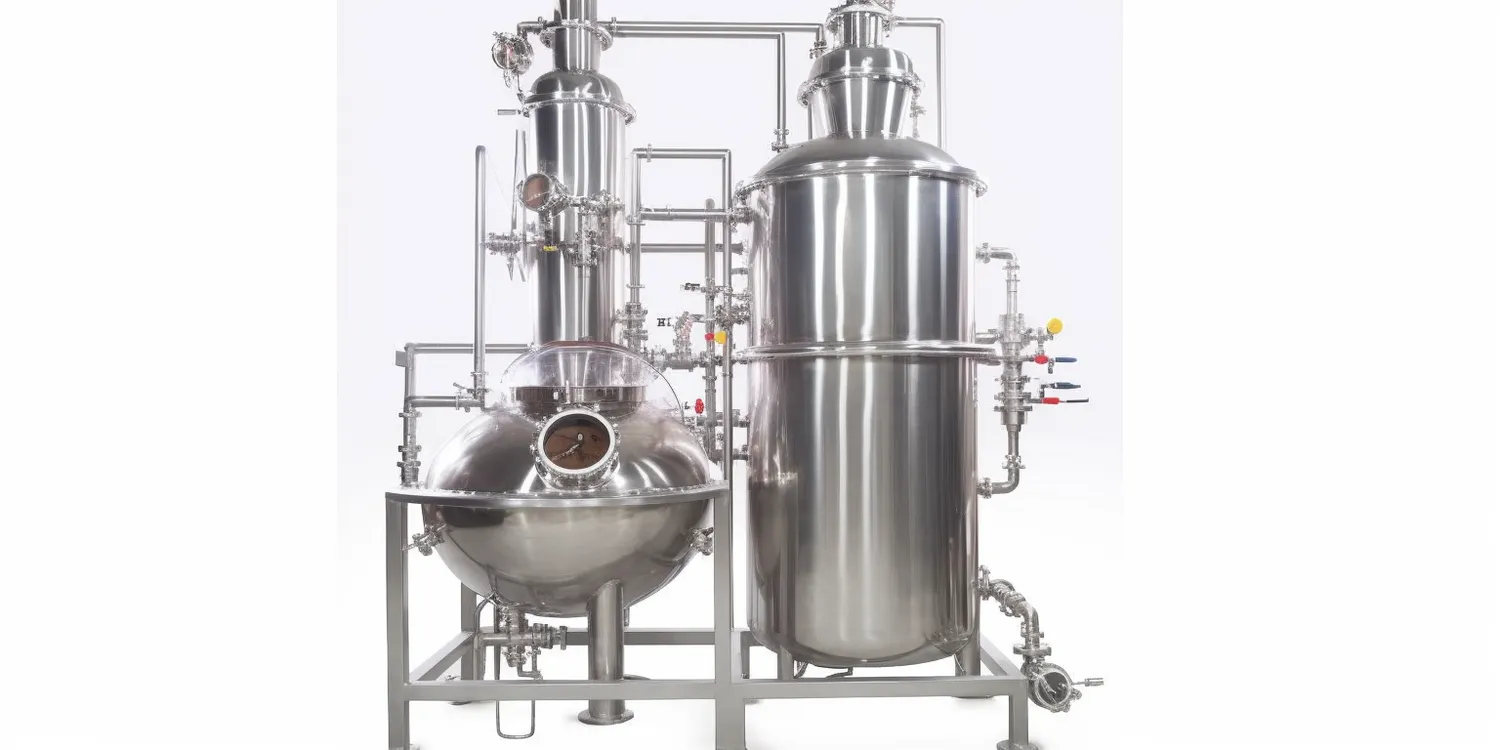
Budowa destylarki do rozpuszczalników wymaga zastosowania odpowiednich materiałów, które będą odporne na działanie chemikaliów oraz wysokich temperatur. Najczęściej wykorzystywanym materiałem jest szkło borokrzemowe, które charakteryzuje się wysoką odpornością na zmiany temperatury oraz działanie agresywnych substancji chemicznych. Szkło to jest powszechnie stosowane w laboratoriach ze względu na swoją przejrzystość, co umożliwia obserwację procesu destylacji. W przypadku przemysłowych aplikacji często stosuje się stal nierdzewną lub inne metale odporne na korozję, które zapewniają trwałość i bezpieczeństwo użytkowania. Dodatkowo niektóre elementy destylarek mogą być pokryte specjalnymi powłokami ochronnymi, które zwiększają ich odporność na działanie chemikaliów. Ważnym aspektem jest również izolacja termiczna urządzenia, która pozwala na efektywne utrzymanie temperatury oraz minimalizuje straty energii podczas procesu destylacji.
Jakie są kluczowe czynniki wpływające na wydajność destylacji
Wydajność procesu destylacji w dużej mierze zależy od kilku kluczowych czynników, które należy uwzględnić przy korzystaniu z destylarki do rozpuszczalników. Przede wszystkim temperatura wrzenia substancji ma ogromny wpływ na efektywność separacji składników. Im większa różnica temperatur wrzenia między poszczególnymi substancjami, tym łatwiejsze będzie ich oddzielenie. Kolejnym istotnym czynnikiem jest czas trwania procesu destylacji; zbyt krótki czas może prowadzić do niepełnej separacji składników, podczas gdy zbyt długi czas może skutkować utratą cennych substancji przez ich dalsze parowanie. Również prędkość podgrzewania cieczy ma znaczenie; zbyt szybkie podgrzewanie może prowadzić do niekontrolowanego parowania i obniżenia jakości uzyskanego produktu. Oprócz tego konstrukcja samej destylarki oraz zastosowane materiały mogą wpływać na efektywność procesu; dobrze zaprojektowana kolumna frakcyjna czy odpowiednia izolacja termiczna mogą znacząco poprawić wyniki destylacji.
Jakie są najczęstsze błędy przy używaniu destylarki do rozpuszczalników
Użytkowanie destylarki do rozpuszczalników wiąże się z pewnymi ryzykami, a nieodpowiednie podejście do procesu może prowadzić do wielu błędów, które mogą wpłynąć na jakość uzyskanego produktu. Jednym z najczęstszych błędów jest niewłaściwe ustawienie temperatury. Użytkownicy często nie dostosowują temperatury wrzenia do specyfiki separowanych substancji, co może prowadzić do ich niepełnej destylacji lub degradacji. Kolejnym problemem jest zbyt szybkie podgrzewanie cieczy, co może skutkować niekontrolowanym parowaniem i stratami cennych składników. Ważne jest również, aby regularnie kontrolować ciśnienie w systemie; jego zmiany mogą wpływać na efektywność procesu. Inny błąd to zaniedbanie czyszczenia destylarki po każdym użyciu, co może prowadzić do zanieczyszczenia kolejnych partii rozpuszczalników. Użytkownicy powinni również zwracać uwagę na odpowiednie uszczelnienie wszystkich połączeń, aby uniknąć wycieków i utraty substancji.
Jakie są korzyści z używania destylarki do rozpuszczalników w laboratoriach
Wykorzystanie destylarki do rozpuszczalników w laboratoriach przynosi szereg korzyści, które znacząco wpływają na jakość prowadzonych badań oraz procesów produkcyjnych. Przede wszystkim umożliwia ona uzyskanie wysokiej czystości substancji chemicznych, co jest kluczowe w wielu eksperymentach i analizach. Dzięki zastosowaniu destylacji można skutecznie oddzielić zanieczyszczenia oraz inne składniki, co pozwala na dokładniejsze wyniki badań. Ponadto destylarka pozwala na recykling rozpuszczalników, co przyczynia się do zmniejszenia kosztów operacyjnych oraz ograniczenia negatywnego wpływu na środowisko. W laboratoriach często zachodzi potrzeba wielokrotnego wykorzystania tych samych substancji chemicznych, a proces destylacji umożliwia ich oczyszczenie i ponowne użycie. Dodatkowo nowoczesne destylarki są wyposażone w zaawansowane systemy monitorowania i kontroli, co zwiększa bezpieczeństwo i efektywność pracy.
Jakie są zasady bezpieczeństwa przy pracy z destylarką do rozpuszczalników
Praca z destylarką do rozpuszczalników wymaga przestrzegania określonych zasad bezpieczeństwa, które mają na celu ochronę zdrowia użytkowników oraz minimalizację ryzyka wystąpienia niebezpiecznych sytuacji. Przede wszystkim należy zawsze stosować odpowiednią odzież ochronną, taką jak rękawice, okulary ochronne oraz fartuchy laboratoryjne, aby zminimalizować kontakt ze szkodliwymi substancjami chemicznymi. Ważne jest również zapewnienie odpowiedniej wentylacji w miejscu pracy; wiele rozpuszczalników wydziela opary, które mogą być toksyczne lub łatwopalne. Użytkownicy powinni być świadomi właściwego postępowania w przypadku awarii lub wycieku; znajomość procedur ewakuacyjnych oraz lokalizacja sprzętu gaśniczego są kluczowe dla bezpieczeństwa. Należy również regularnie kontrolować stan techniczny urządzenia; wszelkie oznaki uszkodzeń powinny być natychmiast zgłaszane i naprawiane przez wykwalifikowany personel. Oprócz tego istotne jest przestrzeganie instrukcji obsługi dostarczonej przez producenta oraz korzystanie z urządzenia zgodnie z jego przeznaczeniem.
Jakie są koszty zakupu i eksploatacji destylarki do rozpuszczalników
Koszty związane z zakupem i eksploatacją destylarki do rozpuszczalników mogą się znacznie różnić w zależności od jej rodzaju, przeznaczenia oraz producenta. Na rynku dostępne są zarówno proste modele laboratoryjne, których cena zaczyna się od kilku tysięcy złotych, jak i bardziej zaawansowane urządzenia przemysłowe, które mogą kosztować kilkadziesiąt tysięcy złotych lub więcej. Wybór odpowiedniej destylarki powinien być uzależniony od specyfiki pracy oraz potrzeb użytkownika; tańsze modele mogą być wystarczające dla małych laboratoriów czy hobbystów, podczas gdy większe zakłady produkcyjne będą wymagały bardziej skomplikowanych systemów o wyższej wydajności. Koszty eksploatacji obejmują nie tylko zużycie energii elektrycznej potrzebnej do podgrzewania cieczy, ale także regularne zakupy materiałów eksploatacyjnych oraz konserwację urządzenia. Warto również uwzględnić koszty związane z utylizacją odpadów chemicznych powstałych w wyniku procesu destylacji.
Jakie innowacje technologiczne wpływają na rozwój destylarek do rozpuszczalników
W ostatnich latach obserwuje się dynamiczny rozwój technologii związanych z produkcją i użytkowaniem destylarek do rozpuszczalników, co przekłada się na ich efektywność oraz bezpieczeństwo pracy. Nowoczesne urządzenia często wyposażane są w zaawansowane systemy automatyzacji i monitorowania procesów, co pozwala na precyzyjne kontrolowanie parametrów pracy oraz minimalizację ryzyka błędów ludzkich. Innowacje te obejmują m.in. inteligentne czujniki temperatury i ciśnienia, które automatycznie dostosowują warunki pracy urządzenia w czasie rzeczywistym. Ponadto rozwijane są nowe materiały konstrukcyjne o zwiększonej odporności chemicznej i termicznej, co wpływa na trwałość urządzeń oraz ich zdolność do pracy w trudnych warunkach. Coraz częściej stosowane są także technologie odzysku energii, które pozwalają na zmniejszenie kosztów eksploatacyjnych poprzez wykorzystanie ciepła generowanego podczas procesu destylacji.
Jakie są alternatywy dla tradycyjnej destylacji w oczyszczaniu rozpuszczalników
Chociaż tradycyjna destylacja jest jedną z najpopularniejszych metod oczyszczania rozpuszczalników, istnieją również alternatywy, które mogą być stosowane w różnych sytuacjach. Jedną z takich metod jest ekstrakcja cieczy cieczą (LLE), która polega na wykorzystaniu dwóch niemieszających się cieczy do oddzielania składników chemicznych na podstawie ich różnej rozpuszczalności. Ta metoda może być szczególnie skuteczna w przypadku substancji o podobnych temperaturach wrzenia. Inną alternatywą jest adsorpcja, która wykorzystuje materiały adsorpcyjne do wychwytywania zanieczyszczeń z roztworów; proces ten może być stosowany zarówno w skali laboratoryjnej, jak i przemysłowej. Filtracja to kolejna metoda oczyszczania substancji chemicznych; poprzez zastosowanie filtrów można skutecznie usunąć cząstki stałe ze cieczy. W ostatnich latach coraz większą popularnością cieszą się także metody membranowe takie jak osmoza odwrotna czy ultrafiltracja; te technologie pozwalają na separację składników chemicznych na podstawie ich wielkości cząsteczek i mogą być stosowane w różnych branżach przemysłowych.