Destylacja rozpuszczalników to proces, który wykorzystuje różnice w temperaturach wrzenia różnych substancji do ich oddzielenia. W praktyce oznacza to, że gdy mieszanina cieczy jest podgrzewana, składniki o niższej temperaturze wrzenia odparowują jako pierwsze. Proces ten jest szeroko stosowany w laboratoriach chemicznych oraz w przemyśle, gdzie czystość rozpuszczalników jest kluczowa dla jakości końcowego produktu. Aby przeprowadzić destylację, niezbędne jest posiadanie odpowiedniego sprzętu, takiego jak kolumna destylacyjna, chłodnica oraz naczynie odbierające. Właściwe ustawienie temperatury i ciśnienia ma kluczowe znaczenie dla efektywności procesu. W przypadku destylacji prostej, która jest najczęściej stosowana w laboratoriach, można uzyskać jedynie jedną frakcję czystego rozpuszczalnika. Natomiast w przypadku destylacji frakcyjnej możliwe jest oddzielenie wielu składników z mieszaniny, co czyni ten proces bardziej skomplikowanym, ale również bardziej efektywnym.
Jakie są zastosowania destylacji rozpuszczalników w przemyśle
Destylacja rozpuszczalników znajduje szerokie zastosowanie w różnych gałęziach przemysłu, od farmaceutycznego po petrochemiczny. W przemyśle chemicznym proces ten jest wykorzystywany do oczyszczania surowców oraz produktów końcowych. Na przykład w produkcji leków ważne jest, aby używane rozpuszczalniki były wolne od zanieczyszczeń, co można osiągnąć poprzez destylację. W przemyśle naftowym destylacja jest kluczowym etapem w procesie rafinacji ropy naftowej, gdzie różne frakcje są oddzielane na podstawie ich temperatur wrzenia. To pozwala na uzyskanie paliw o różnych właściwościach oraz innych produktów naftowych. W branży spożywczej destylacja służy do produkcji alkoholu oraz ekstrakcji aromatów z roślin. Dzięki temu możliwe jest uzyskanie wysokiej jakości produktów, które spełniają normy jakościowe i zdrowotne.
Jakie są różnice między destylacją prostą a frakcyjną
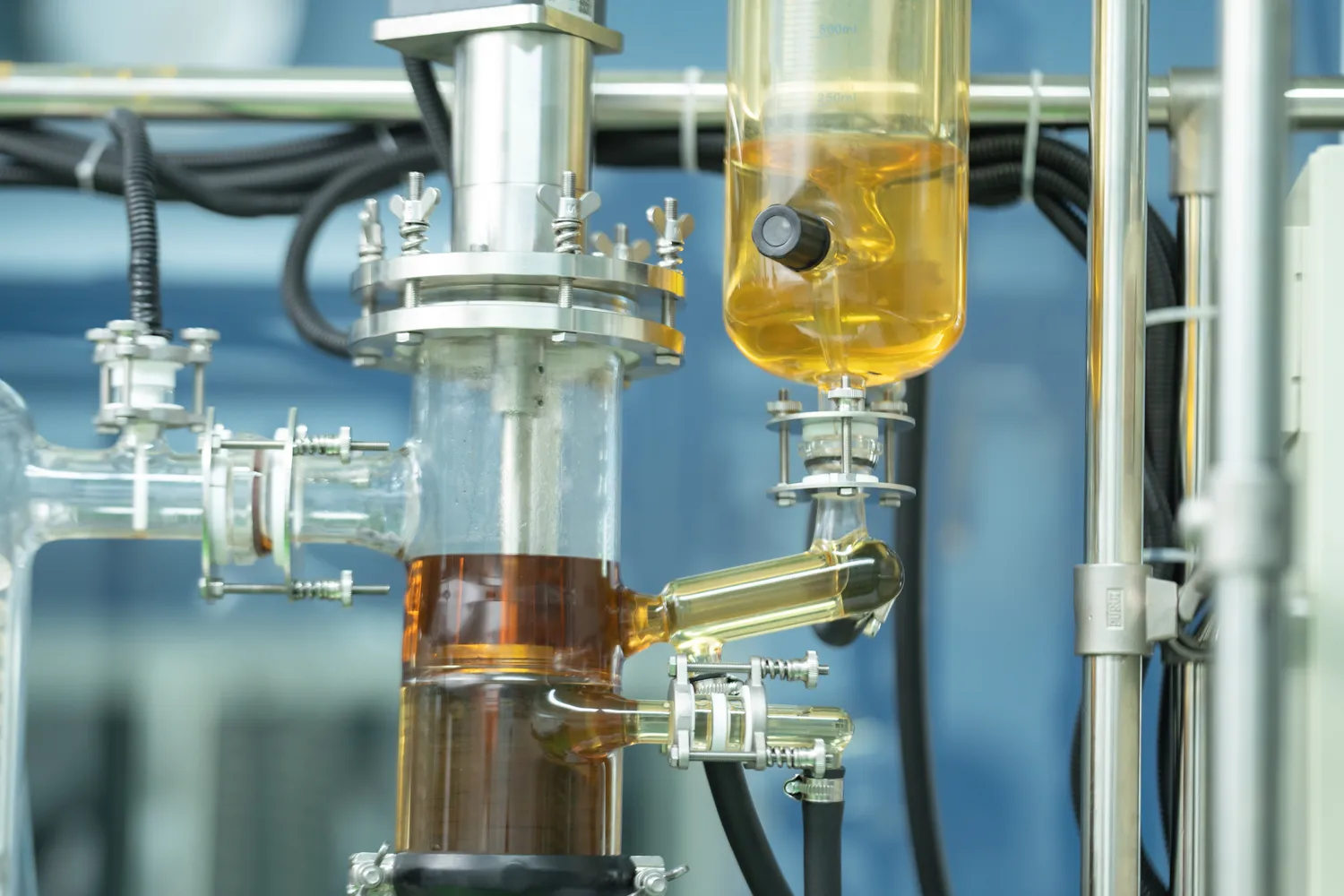
Destylacja prosta i frakcyjna to dwa podstawowe rodzaje procesów destylacyjnych, które różnią się zarówno techniką wykonania, jak i zastosowaniami. Destylacja prosta polega na podgrzewaniu mieszaniny cieczy do momentu, gdy jedna z jej frakcji zaczyna wrzeć i odparowywać. Opary są następnie schładzane i kondensowane z powrotem do stanu ciekłego. Ten typ destylacji sprawdza się najlepiej w przypadku mieszanin zawierających substancje o znacznie różniących się temperaturach wrzenia. Z kolei destylacja frakcyjna jest bardziej skomplikowanym procesem, który wykorzystuje kolumnę destylacyjną do wielokrotnego skraplania i odparowywania cieczy. Dzięki temu możliwe jest uzyskanie kilku frakcji o różnych składach chemicznych z jednej mieszaniny. Destylacja frakcyjna jest szczególnie przydatna w przypadku substancji o zbliżonych temperaturach wrzenia, gdzie separacja wymaga większej precyzji.
Jakie są najczęstsze błędy podczas destylacji rozpuszczalników
Podczas przeprowadzania procesu destylacji rozpuszczalników mogą wystąpić różne błędy, które mogą wpłynąć na jakość uzyskanego produktu. Jednym z najczęstszych błędów jest niewłaściwe ustawienie temperatury grzania, co może prowadzić do niepełnej separacji składników lub ich degradacji. Zbyt wysoka temperatura może spowodować przegrzanie cieczy i powstanie niepożądanych produktów ubocznych. Innym problemem może być niewłaściwe dobranie sprzętu do konkretnego procesu destylacyjnego; na przykład użycie kolumny o niewłaściwej wysokości może ograniczyć efektywność separacji frakcji. Ważne jest także monitorowanie ciśnienia wewnętrznego systemu; jego zmiany mogą wpływać na temperatury wrzenia substancji i prowadzić do nieprzewidywalnych rezultatów. Często zdarza się również nieuwaga przy zbieraniu frakcji; jeśli nie zostaną one odpowiednio oznaczone lub skatalogowane, może to prowadzić do pomyłek w późniejszych analizach czy eksperymentach.
Jakie są kluczowe czynniki wpływające na efektywność destylacji rozpuszczalników
Efektywność destylacji rozpuszczalników zależy od wielu czynników, które mogą znacząco wpłynąć na jakość i ilość uzyskanego produktu. Jednym z najważniejszych aspektów jest temperatura wrzenia poszczególnych składników mieszaniny. Różnice w temperaturach wrzenia pozwalają na selektywne odparowanie konkretnych substancji, co jest kluczowe dla skutecznej separacji. Warto również zwrócić uwagę na ciśnienie atmosferyczne, które może modyfikować temperatury wrzenia substancji; w warunkach obniżonego ciśnienia substancje mogą wrzeć w niższych temperaturach, co może być korzystne w przypadku delikatnych związków chemicznych. Kolejnym czynnikiem jest czas trwania destylacji; zbyt krótki czas może prowadzić do niepełnej separacji, podczas gdy zbyt długi czas może skutkować degradacją składników. Właściwe dobranie sprzętu destylacyjnego, takiego jak kolumny czy chłodnice, również ma kluczowe znaczenie dla efektywności procesu.
Jakie są różnice między destylacją a innymi metodami oczyszczania
Destylacja jest jedną z wielu metod oczyszczania substancji chemicznych, jednak różni się od innych technik zarówno zasadą działania, jak i zastosowaniem. Na przykład filtracja to proces mechaniczny, który polega na oddzieleniu ciał stałych od cieczy za pomocą materiału filtracyjnego. Jest to metoda stosunkowo prosta i szybka, ale nieefektywna w przypadku rozdzielania cieczy o podobnych właściwościach fizykochemicznych. Z kolei ekstrakcja wykorzystuje różnice w rozpuszczalności substancji w różnych rozpuszczalnikach do ich oddzielenia; ta metoda jest szczególnie przydatna w przypadku substancji organicznych. W przeciwieństwie do tych metod, destylacja opiera się na różnicach temperatur wrzenia i jest bardziej skomplikowana, ale pozwala na uzyskanie wyższej czystości produktów. Inną popularną metodą oczyszczania jest chromatografia, która wykorzystuje różnice w adsorpcji lub rozpuszczalności substancji w różnych fazach do ich separacji. Choć chromatografia może być bardziej czasochłonna i kosztowna, często daje lepsze wyniki w przypadku bardzo skomplikowanych mieszanin.
Jakie są najnowsze osiągnięcia technologiczne w dziedzinie destylacji
W ostatnich latach dziedzina destylacji rozpuszczalników przeszła znaczne zmiany dzięki nowym technologiom i innowacjom. Jednym z najważniejszych osiągnięć jest rozwój bardziej efektywnych kolumn destylacyjnych, które pozwalają na lepszą separację frakcji przy mniejszym zużyciu energii. Nowoczesne kolumny wyposażone są w zaawansowane systemy kontroli temperatury i ciśnienia, co umożliwia precyzyjne dostosowanie warunków procesu do specyfiki danej mieszaniny. Ponadto coraz częściej stosuje się technologię membranową, która pozwala na separację składników bez konieczności podgrzewania ich do wysokich temperatur. To podejście nie tylko zmniejsza zużycie energii, ale także minimalizuje ryzyko degradacji delikatnych substancji chemicznych. Innowacje obejmują także zastosowanie sztucznej inteligencji i algorytmów uczenia maszynowego do optymalizacji procesów destylacyjnych; dzięki tym technologiom możliwe jest przewidywanie zachowań mieszanin oraz automatyczne dostosowywanie parametrów procesu.
Jakie są ekologiczne aspekty związane z procesem destylacji rozpuszczalników
Ekologiczne aspekty związane z procesem destylacji rozpuszczalników stają się coraz ważniejsze w kontekście globalnych działań na rzecz ochrony środowiska. Proces ten często wiąże się z dużym zużyciem energii oraz emisją gazów cieplarnianych, co stawia przed przemysłem chemicznym wyzwanie związane z redukcją śladu węglowego. Dlatego wiele firm zaczyna wdrażać bardziej zrównoważone praktyki produkcyjne, takie jak wykorzystanie odnawialnych źródeł energii do podgrzewania kolumn destylacyjnych czy optymalizacja procesów w celu zmniejszenia zużycia energii. Ponadto rośnie zainteresowanie recyklingiem rozpuszczalników organicznych; proces ten polega na odzyskiwaniu użytych rozpuszczalników poprzez ich destylację i ponowne wykorzystanie w produkcji. Takie podejście nie tylko ogranicza ilość odpadów chemicznych, ale także zmniejsza zapotrzebowanie na nowe surowce. Warto również zauważyć, że rozwój nowych technologii destylacyjnych, takich jak membrany czy systemy osmozy, może przyczynić się do dalszej redukcji negatywnego wpływu na środowisko.
Jakie są perspektywy rozwoju technologii destylacji rozpuszczalników
Perspektywy rozwoju technologii destylacji rozpuszczalników wydają się obiecujące dzięki ciągłym innowacjom oraz rosnącemu zapotrzebowaniu na czyste i efektywne procesy produkcyjne. W miarę jak przemysł chemiczny staje przed wyzwaniami związanymi z ochroną środowiska oraz potrzebą zwiększenia efektywności energetycznej, technologie związane z destylacją będą musiały ewoluować. Możliwości zastosowania sztucznej inteligencji oraz automatyzacji procesów produkcyjnych otwierają nowe horyzonty dla optymalizacji procesów destylacyjnych; dzięki tym technologiom można przewidywać zmiany zachodzące w mieszaninach oraz automatycznie dostosowywać parametry operacyjne do aktualnych potrzeb produkcyjnych. Dodatkowo rozwój materiałów o lepszych właściwościach termicznych i mechanicznych może przyczynić się do budowy bardziej wydajnych kolumn destylacyjnych oraz systemów chłodniczych. Warto również zauważyć rosnące zainteresowanie ekologicznymi aspektami produkcji chemicznej; przedsiębiorstwa będą musiały inwestować w technologie pozwalające na redukcję emisji oraz minimalizację zużycia surowców naturalnych.
Jakie są najczęstsze zastosowania przemysłowe dla różnych rodzajów rozpuszczalników
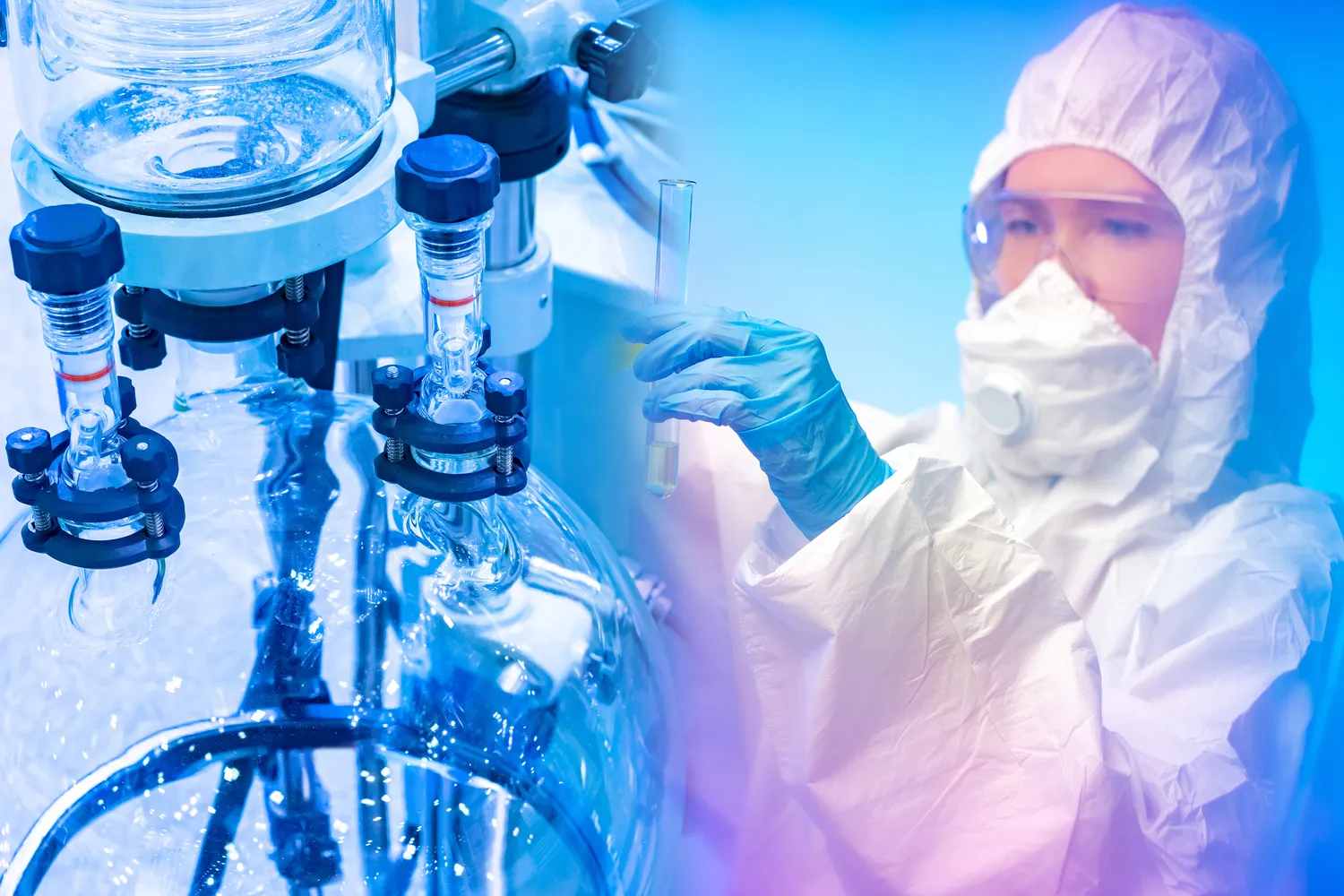

Rozpuszczalniki znajdują szerokie zastosowanie w różnych gałęziach przemysłu ze względu na swoje unikalne właściwości chemiczne i fizyczne. W przemyśle farmaceutycznym wykorzystywane są głównie do syntez chemicznych oraz jako nośniki dla substancji aktywnych; ich czystość jest kluczowa dla bezpieczeństwa leków. W branży kosmetycznej rozpuszczalniki służą do tworzenia emulsji oraz jako składniki aktywne w produktach pielęgnacyjnych; ich właściwości wpływają na konsystencję i skuteczność działania kosmetyków. Przemysł farbiarski korzysta z różnych rodzajów rozpuszczalników organicznych do rozcieńczania farb i lakierów; odpowiedni dobór rozpuszczalnika ma kluczowe znaczenie dla jakości powłok malarskich oraz ich trwałości. W przemyśle petrochemicznym rozpuszczalniki są wykorzystywane do ekstrakcji olejków eterycznych oraz jako składniki paliw; ich właściwości wpływają na wydajność spalania oraz emisję spalin.