Budowa maszyn pneumatycznych opiera się na kilku kluczowych elementach, które są niezbędne do ich prawidłowego funkcjonowania. Wśród najważniejszych komponentów można wymienić sprężarki, które odpowiadają za wytwarzanie sprężonego powietrza. Sprężone powietrze jest następnie transportowane do różnych części maszyny, gdzie jest wykorzystywane do wykonywania pracy mechanicznej. Kolejnym istotnym elementem są zawory, które kontrolują przepływ powietrza w systemie. Dzięki nim możliwe jest precyzyjne sterowanie ruchem siłowników pneumatycznych. Siłowniki to kolejny kluczowy komponent, który przekształca energię sprężonego powietrza w ruch mechaniczny. W zależności od zastosowania mogą mieć różne konstrukcje i rozmiary. Oprócz tych podstawowych elementów, w budowie maszyn pneumatycznych znajdują się również filtry, które oczyszczają powietrze z zanieczyszczeń oraz zbiorniki, które magazynują sprężone powietrze, co pozwala na stabilizację ciśnienia w systemie.
Jakie są zastosowania maszyn pneumatycznych w przemyśle
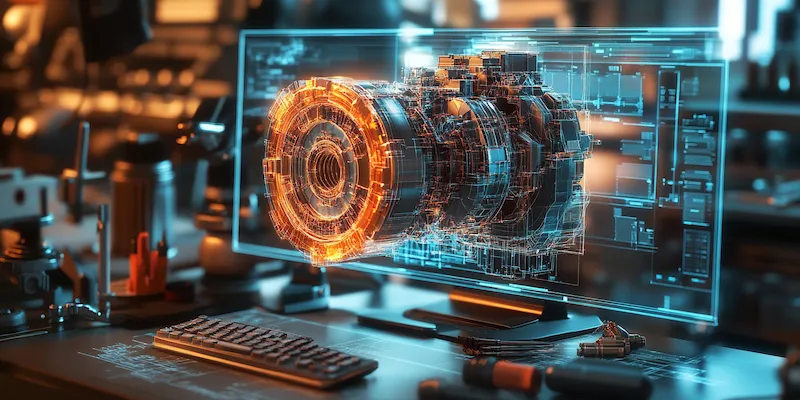
Maszyny pneumatyczne znajdują szerokie zastosowanie w różnych gałęziach przemysłu, co czyni je niezwykle wszechstronnymi narzędziami. W branży produkcyjnej wykorzystuje się je do automatyzacji procesów montażowych, gdzie precyzyjne ruchy siłowników pneumatycznych przyspieszają i usprawniają pracę linii produkcyjnych. W przemyśle spożywczym maszyny te są używane do pakowania produktów oraz transportu materiałów sypkich, co zapewnia efektywność i higienę procesu. W sektorze budowlanym maszyny pneumatyczne służą do obsługi narzędzi takich jak młoty udarowe czy wiertnice, co zwiększa wydajność pracy na placu budowy. Dodatkowo, w przemyśle motoryzacyjnym stosuje się je do testowania szczelności oraz montażu podzespołów. Ich zaletą jest również możliwość pracy w trudnych warunkach, gdzie inne źródła energii mogą zawodzić.
Jakie są zalety i wady maszyn pneumatycznych
Maszyny pneumatyczne mają wiele zalet, które sprawiają, że są one atrakcyjnym wyborem dla wielu przedsiębiorstw. Jedną z głównych korzyści jest ich prostota obsługi oraz niskie koszty eksploatacji. Sprężone powietrze jest powszechnie dostępnym medium energetycznym, a jego wykorzystanie nie wymaga skomplikowanych instalacji elektrycznych czy hydraulicznych. Ponadto maszyny te charakteryzują się dużą niezawodnością oraz długą żywotnością, co przekłada się na mniejsze koszty serwisowania i napraw. Jednakże istnieją również pewne ograniczenia związane z ich użytkowaniem. Maszyny pneumatyczne mogą być mniej efektywne w porównaniu do systemów hydraulicznych przy wykonywaniu zadań wymagających dużej siły lub precyzyjnego sterowania. Dodatkowo sprężone powietrze może być podatne na straty energii podczas transportu przez przewody, co wpływa na ogólną efektywność systemu.
Jakie innowacje wpływają na rozwój budowy maszyn pneumatycznych
W ostatnich latach obserwuje się dynamiczny rozwój technologii związanych z budową maszyn pneumatycznych, co ma znaczący wpływ na ich efektywność i zastosowanie w różnych branżach. Innowacje te obejmują między innymi rozwój nowoczesnych materiałów oraz technologii produkcji komponentów. Dzięki zastosowaniu lekkich i wytrzymałych materiałów możliwe jest tworzenie bardziej kompaktowych i wydajnych siłowników oraz zaworów. Ponadto automatyzacja procesów produkcyjnych pozwala na zwiększenie precyzji wykonania poszczególnych elementów maszyn pneumatycznych. Również rozwój technologii cyfrowych wpływa na sposób zarządzania systemami pneumatycznymi; inteligentne czujniki oraz systemy monitoringu umożliwiają bieżące śledzenie parametrów pracy maszyn oraz szybką reakcję na ewentualne awarie. Zastosowanie sztucznej inteligencji i analizy danych pozwala na optymalizację procesów produkcyjnych oraz zwiększenie efektywności energetycznej systemów pneumatycznych.
Jakie są kluczowe wyzwania w budowie maszyn pneumatycznych
Budowa maszyn pneumatycznych wiąże się z wieloma wyzwaniami, które inżynierowie i projektanci muszą pokonywać, aby zapewnić ich efektywność i niezawodność. Jednym z głównych problemów jest zarządzanie ciśnieniem sprężonego powietrza. Utrzymanie odpowiedniego poziomu ciśnienia jest kluczowe dla prawidłowego działania systemu, a jego wahania mogą prowadzić do awarii lub obniżenia wydajności maszyny. Kolejnym wyzwaniem jest minimalizacja strat energii, które mogą występować podczas transportu sprężonego powietrza przez przewody. Straty te mogą być spowodowane niewłaściwym doborem średnicy rur, nieszczelnościami czy nieefektywnymi zaworami. Dodatkowo, w kontekście rosnących wymagań dotyczących ochrony środowiska, projektanci muszą dążyć do zmniejszenia hałasu generowanego przez maszyny pneumatyczne oraz do ograniczenia emisji substancji szkodliwych. Wyzwania te wymagają innowacyjnych rozwiązań technologicznych oraz ciągłego doskonalenia procesów produkcyjnych.
Jakie są różnice między maszynami pneumatycznymi a hydraulicznymi
Maszyny pneumatyczne i hydrauliczne to dwa różne systemy wykorzystywane w automatyce przemysłowej, które mają swoje unikalne cechy oraz zastosowania. Główna różnica między nimi polega na medium roboczym; maszyny pneumatyczne wykorzystują sprężone powietrze, podczas gdy maszyny hydrauliczne działają na zasadzie cieczy hydraulicznej. Ta różnica wpływa na sposób działania obu systemów oraz ich efektywność w różnych aplikacjach. Maszyny pneumatyczne są zazwyczaj lżejsze i prostsze w budowie, co sprawia, że są łatwiejsze do zainstalowania i konserwacji. Z drugiej strony, maszyny hydrauliczne oferują większą siłę i precyzję, co czyni je bardziej odpowiednimi do zadań wymagających dużych obciążeń lub skomplikowanych ruchów. Kolejnym aspektem jest koszt eksploatacji; sprężone powietrze jest tańsze niż ciecz hydrauliczna, co sprawia, że maszyny pneumatyczne mogą być bardziej ekonomiczne w dłuższej perspektywie. Jednakże systemy hydrauliczne często charakteryzują się lepszą wydajnością energetyczną przy dużych obciążeniach.
Jakie są przyszłe kierunki rozwoju technologii maszyn pneumatycznych
Przyszłość technologii maszyn pneumatycznych zapowiada się obiecująco dzięki ciągłemu postępowi technologicznemu oraz rosnącemu zapotrzebowaniu na automatyzację procesów przemysłowych. Wśród kluczowych kierunków rozwoju można wymienić integrację systemów pneumatycznych z nowoczesnymi technologiami cyfrowymi. Wprowadzenie Internetu Rzeczy (IoT) do maszyn pneumatycznych umożliwi monitorowanie ich pracy w czasie rzeczywistym oraz zdalne zarządzanie procesami produkcyjnymi. Dzięki temu przedsiębiorstwa będą mogły szybciej reagować na ewentualne problemy oraz optymalizować zużycie energii. Kolejnym trendem jest rozwój inteligentnych siłowników pneumatycznych, które będą mogły dostosowywać swoją pracę do zmieniających się warunków operacyjnych. Innowacje w zakresie materiałów również mają duże znaczenie; nowe kompozyty i materiały o wysokiej wytrzymałości mogą przyczynić się do zwiększenia efektywności maszyn oraz ich odporności na uszkodzenia. Ponadto, coraz większy nacisk kładzie się na zrównoważony rozwój i ekologiczne aspekty produkcji; inżynierowie pracują nad rozwiązaniami zmniejszającymi hałas oraz emisję substancji szkodliwych związanych z użytkowaniem maszyn pneumatycznych.
Jakie są najczęstsze błędy przy projektowaniu maszyn pneumatycznych
Projektowanie maszyn pneumatycznych to skomplikowany proces, który wymaga uwzględnienia wielu czynników technicznych i praktycznych. Niestety, istnieje wiele pułapek, w które mogą wpaść inżynierowie podczas tego procesu. Jednym z najczęstszych błędów jest niewłaściwe dobranie komponentów do specyfikacji projektu; użycie elementów o niewłaściwej wydajności lub parametrach może prowadzić do awarii całego systemu lub jego niskiej efektywności. Kolejnym powszechnym problemem jest brak odpowiednich zabezpieczeń przed nadmiernym ciśnieniem lub innymi niebezpiecznymi sytuacjami; niewłaściwe zabezpieczenia mogą prowadzić do poważnych awarii i zagrożeń dla bezpieczeństwa operatorów. Inżynierowie często zaniedbują także kwestie związane z konserwacją i serwisowaniem maszyn; projektując systemy bez uwzględnienia łatwego dostępu do kluczowych komponentów, mogą utrudnić przyszłe naprawy i przeglądy. Dodatkowo, błędy w obliczeniach dotyczących przepływu powietrza czy ciśnienia mogą prowadzić do nieoptymalnego działania systemu.
Jakie są najlepsze praktyki w eksploatacji maszyn pneumatycznych
Aby zapewnić długotrwałe i efektywne działanie maszyn pneumatycznych, konieczne jest przestrzeganie najlepszych praktyk podczas ich eksploatacji. Kluczowym elementem jest regularne przeprowadzanie konserwacji oraz przeglądów technicznych; pozwala to na wykrycie ewentualnych usterek zanim staną się one poważnym problemem. Ważne jest również monitorowanie parametrów pracy systemu, takich jak ciśnienie czy temperatura sprężonego powietrza; wszelkie odchylenia od normy powinny być natychmiast analizowane i korygowane. Użytkownicy powinni także zwracać uwagę na jakość sprężonego powietrza; stosowanie filtrów oraz separatorów kondensatu pomoże uniknąć zanieczyszczeń wpływających negatywnie na działanie maszyn. Dodatkowo warto inwestować w szkolenia dla pracowników obsługujących maszyny pneumatyczne; dobrze przeszkolony personel będzie bardziej świadomy potencjalnych zagrożeń oraz umiejętności niezbędnych do prawidłowej obsługi urządzeń.
Jakie są trendy w automatyzacji procesów związanych z maszynami pneumatycznymi
Automatyzacja procesów związanych z maszynami pneumatycznymi staje się coraz bardziej popularna dzięki rosnącym wymaganiom rynku oraz potrzebom przedsiębiorstw dążących do zwiększenia efektywności produkcji. Jednym z najważniejszych trendów jest integracja systemów pneumatycznych z robotyką; współpraca robotów z urządzeniami pneumatycznymi pozwala na automatyzację skomplikowanych procesów montażowych czy pakujących, co znacznie zwiększa wydajność linii produkcyjnych. Również rozwój sztucznej inteligencji ma ogromny wpływ na automatyzację; inteligentne algorytmy umożliwiają optymalizację pracy maszyn poprzez analizę danych zbieranych podczas ich działania oraz prognozowanie ewentualnych awarii czy potrzeb serwisowych.